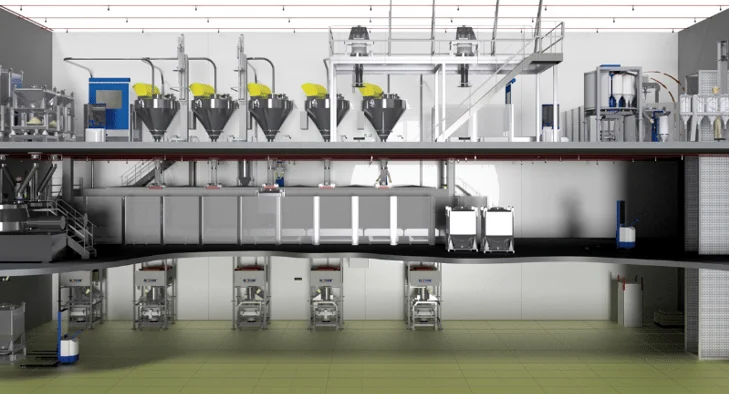
HANDLING BATTERY POWDERS
Modular Systems for Battery Material Manufacturing
Tried and tested equipment that can deliver product consistency and contained transfer at all stages. Specifically tailored for the challenging conditions of battery production, our modular systems employ Intermediate Bulk Containers (IBCs). This strategy streamlines production workflow but also significantly reduces the risk of contamination and loss of materials, thereby ensuring the high quality of the final product.
SAFE, EFFICIENT, SCALABLE
Key Features of a Matcon System:
- Cone Valve Technology: Our proprietary Cone Valve technology is central to the effective handling of difficult flowing or segregation-prone powders, enhancing your production's safety and reliability.
- Modular Design: Designed for versatility, our IBCs offer a customisable and scalable solution, ensuring our systems grow with your manufacturing demands.
- Automated Material Transfer: Automation is at the forefront, facilitating seamless, contained transfer of hazardous and innocuous powders between stages and reducing manual handling.
- Expert Connections: Designed with the battery manufacturing process in mind, expertly engineered connections offer unrivalled containment and transfer, even at the most critical stages.
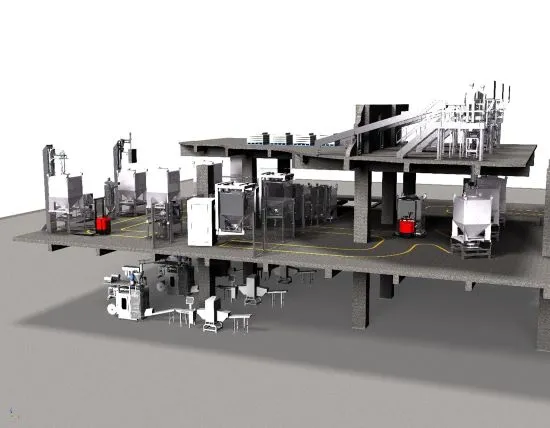
IBC Range
Matcon are experts in creating powder handling systems optimised to achieve superior manufacturing efficiency. Solutions are based on our unique Cone Valve Intermediate Bulk Containers (IBCs) which are used to move materials between manufacturing steps or for processing & blending powders.
Our diverse IBC portfolio spans various designs, materials, and capacities, all featuring our proprietary Cone Valve Technology. These containers ensure precise flow control, prevent moisture ingress, accommodate temperature variations, and offer numerous capacity options.
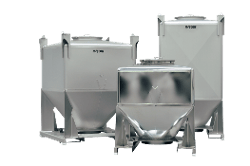
Stainless Steel IBCs
The Matcon Cone Valve IBC is available in 316, 304 stainless steel or a lower carbon variant upon request, tailored to suit specific applications. Our design ensures the IBC can withstand pressures ranging from -25 to +50 millibars, optimising flow control and effectively preventing moisture ingress. This feature is critical in maintaining the integrity and quality of sensitive battery powders during the storage and transportation phases.
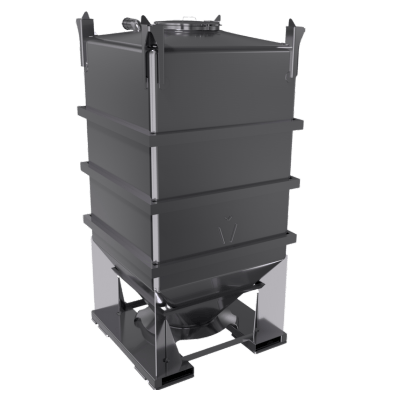
Heavy Duty IBCs
Our Heavy Duty IBCs are specifically designed to meet the robust demands of a gigafactory large-production. Boasting an impressive air capacity of 3700L and able to withstand pressures up to 100 millibars, this model is engineered for high-efficiency operations. Its ability to be stacked addresses the critical need to conserve floor space, making it an ideal solution for facilities where space is at a premium.

Hot Powder IBCs
Our Hot Powder IBCs are engineered to withstand powders at temperatures up to 200 degrees Celsius. This ground-breaking design enables hot powders to be collected from furnaces, reactors, and jet mills and discharged to the downstream process without the need for excessive cooling. Being able to reduce the size and capacity of cooling equipment can result in significant CAPEX savings.
If you are finding it challenging to handle hot battery powders, then these IBCs will ensure materials are handled safely and efficiently without compromising performance or safety standards.

Polyethylene IBCs
For those seeking a more versatile and cost-effective solution, our Polyethylene IBC Range provides an alternative to stainless steel. Equipped with the Matcon Cone Valve technology found in our stainless steel range, these IBCs ensure that powders are discharged under a mass-flow discharge process. Ideal for blending, storage, and transportation of powder materials, our polyethylene IBCs offer a durable, lightweight option.
Discharge Stations
The IBCs are paired with a discharge station which is selected according to the powder material characteristics and the downstream process into which the powder is being fed. Designed to be fully automated, our discharge stations ensure optimal flow control and prevention of material segregation.
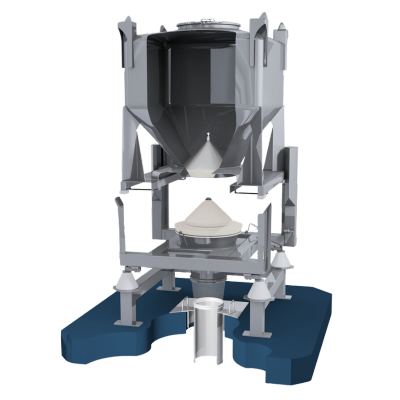
Standard
The Standard Cone Valve Discharge Station will handle most powders and ensures controlled flow of material feed to the process below. At the extremes of the more difficult to handle powders, then additional functionality such as vibration is required to proactively tackle compaction and bridging.
The unique action of the Cone Valve in the outlet of the IBC creates ‘mass flow’ discharge and protects the homogenous material from particle segregation. The consistency of the material can be retained throughout, preserving the quality of the final product.
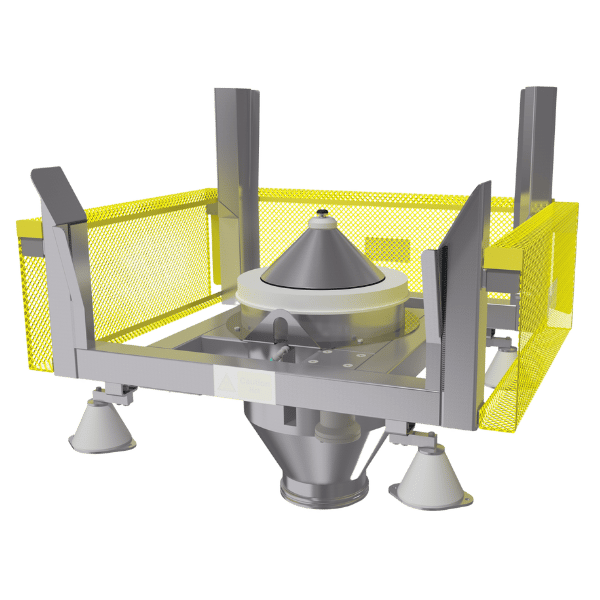
High Temperature
The Hot Powder Discharge Station embodies the features of the standard version with the addition that it is specifically constructed to discharge powders with a temperature up to 200 degrees Celsius.
Until now, powders were cooled down simply because there was no means to handle them at elevated temperatures. Now with the innovative Hot Powder IBC & Discharge Station duo, full cooling may no longer be a process necessity, offering significant CAPEX and OPEX savings.
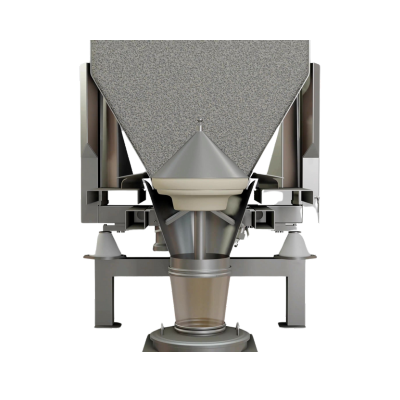
Vari Stroke
For operations that require a more controlled feed or accurate dosing directly from the IBC, the Vari Stroke Discharge Station is an ideal solution. Equipped with an adjustable stroke length that controls the lift height of the Cone Valve in the IBC outlet, this innovative station allows for precise control of powder flow without the need for secondary feeders.
The discharge rate can be configured for a high flow rate at the beginning of the discharge process then reducing the height and pulsing the Cone Valve to achieve a very low flow of powder to ensure the target material weight is achieved.
Blending Product Range
Our blending systems are engineered with maximum flexibility in mind, accommodating a wide variety of powder materials and production requirements. The IBC becomes the blending vessel, ensuring a contained process with no clean-down time needed. These IBCs range from 100L using our Pilot Scale Blender to 3500L at the production scale.
The addition of a High Shear Intensifier extends the range of blending capability into the scope of battery powder fibrillisation.
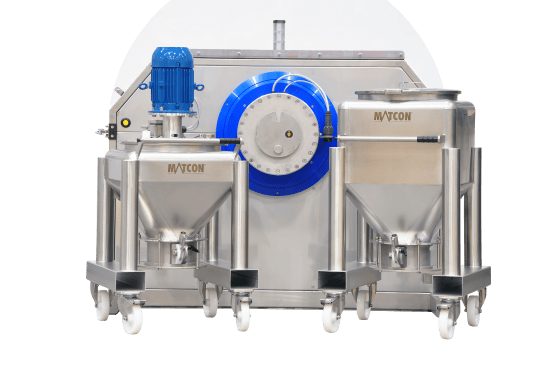
Pilot Scale Blender
The Pilot Scale Blender represents our commitment to supporting battery innovation and the proof of concept stage or enabling the processing of smaller-sized production quantities.
Designed to offer blending operations using IBC sizes ranging from 50 to 200L, it is scalable to the larger IBCs, ensuring a smooth transition from pilot to full-scale production.
Uniquely for this size of mixer, high-shear blending is also available using the intensifier. This is a critical component for rigorous experimentation and scaling in powder fibrillation.
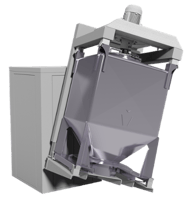
Production Scale Blender
This system is engineered to blend large quantities of powders consistently, ensuring homogeneity and reproducibility throughout the process. Its design allows operators to control the intensity and duration of mixing operations, resulting in an optimal blend every time.
Engineered to cater to a broad spectrum of batch volumes, ranging from 500L to 3,300L, the IBC Blender is designed to meet varying production demands with agility. Batch volumes are tailorable, allowing for IBCs to be filled at anywhere from 20% to 80% of their full capacity, accommodating specific blending requirements.
Additionally, the blending efficacy is expandable through the integration of the Matcon Intensifier, which extends the versatility of tumble blending, notably in the domain of powder fibrillization, enriching the blending application spectrum significantly.
Cleaning Product Range
We understand the importance of maintaining a clean production environment, especially when handling sensitive or hazardous materials. Our cleaning product range is designed with this in mind, providing efficient and effective solutions to keep your facility contamination-free.
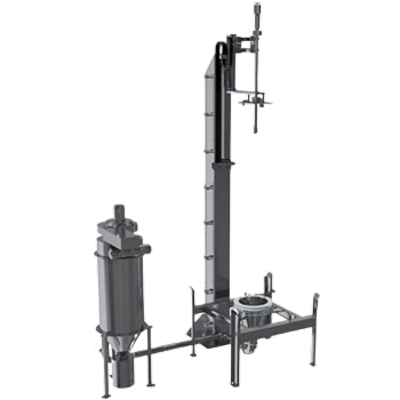
Air Wash Station
Leveraging the power of compressed air, the Air Wash Station excels in efficiently removing any residual dust particles and debris from the inside of the IBC, negating the need for liquid detergents, hot water, or hot air.
One of the standout features of this station is the integration of automatic controls, ensuring ease of use. It comes equipped with a dust extraction unit to collect any residual powder waste.
Battery Developer Hub
Explore the Battery Developer Hub, your premier resource for gaining engineering insights into optimising powder handling in battery production. This dedicated resource offers insightful webcasts and expert engineering solutions. Discover more about our innovative equipment designed to address industry challenges and improve production efficiency. Engineer a better tomorrow, today!
Discover the Battery Developer Hub, your top destination for acquiring engineering knowledge of optimising powder handling in battery manufacturing. This specialised resource provides informative webcasts and expert engineering solutions. Learn more about our cutting-edge equipment designed to tackle industry challenges and enhance production efficiency.