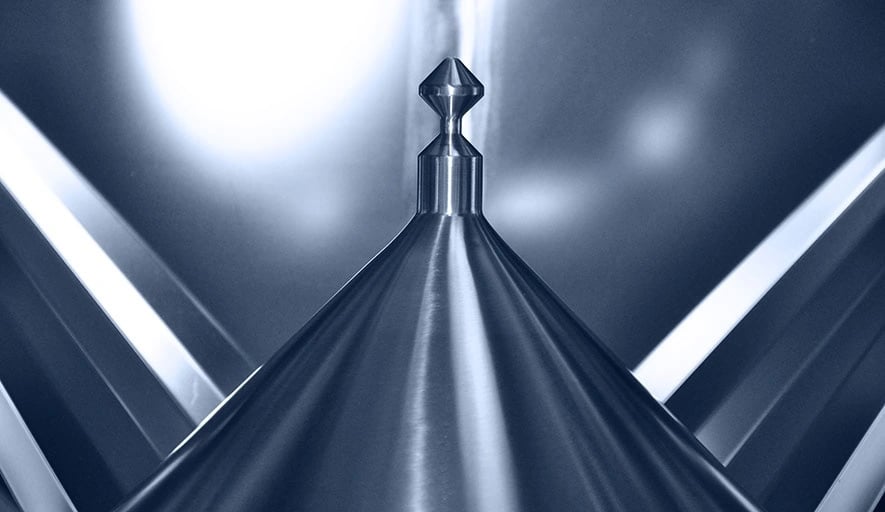
EFFICIENT, EFFECTIVE, FLEXIBLE
IBC Blenders & Industrial Powder Mixers
In-bin blending adds flexibility & agility to any production line. Because the IBC is the blending vessel it means there is no need to clean down between batches, simply switch in a fresh batch IBC.
Tumble blending offers gentle mixing of fragile powders, with the option to add high shear mixing when a more vigorous process is required.
High Containment
Resolves Powder Flow Issues
Improved Efficiency
Powder Handling System Modules
Matcon's blending capabilities are just one element of the efficient powder handling systems we offer. Our processing equipment helps you at every stage of your powder handling process, streamlining your operations, improving product quality and helping increase your margins. By decoupling the manufacturing steps, we enable manufacturers to achieve a flexible and efficient powder handling system.
PROVEN CAPABILITIES
Global Testing Facilities
At Matcon, we want to ensure you have access to the right equipment and specifications you need to produce a high-quality end product. Materials, environment, humidity and powder characteristics all play a huge part in influencing how powders will behave during blending, packing or even in transit. Our state-of-the-art test plants give you the opportunity to test your product mixes with our equipment in a controlled environment.
Test Centres
Our state-of-the-art Test Plants are designed to simulate actual working conditions using your individual recipes, giving you peace of mind that your test results represent real world operations.
United Kingdom
Full-scale equipment capabilities including Near-Infrared (NIR) spectroscopy, allergen swabbing & lab testing equipment.
USA
Full-scale equipment capabilities including blending, formulation & cleaning.
China
Full-scale equipment capabilities including blending, formulation & cleaning.
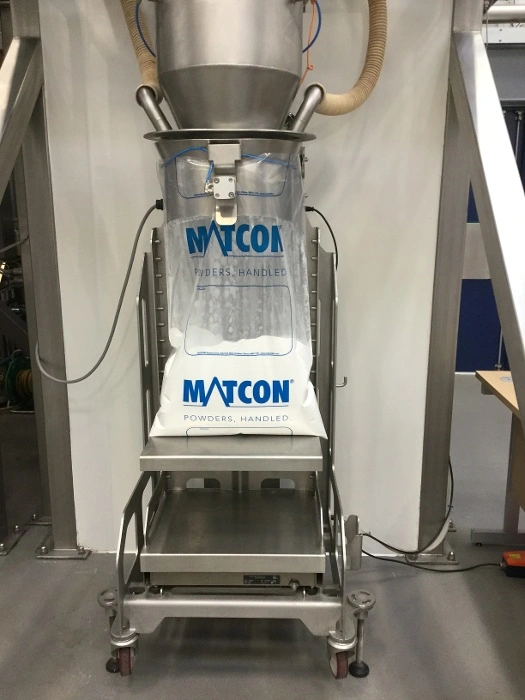