Matcon Aftermarket
At Matcon we are committed to achieving total customer satisfaction before, during and after the installation of your IBC system.
We want you to make the most of your investment so we support you by offering a full range of original spares and a Maintenance Service.
Matcon's Aftermarket team are dedicated to providing technical assistance and guidance. Please contact our team via the form below or view our Frequently Asked Questions.
Spares
Using original spare parts ensures reliability and helps to protect your investment.
We develop, test and update our equipment components to ensure you have the best to keep your equipment running smoothly.
We strive to keep delivery times to a bare minimum as we are mindful of the costs of downtime.
Maintenance
Regularly serviced equipment delivers greater efficiency & reliability than equipment left to run without attention.
Our service engineers have worked on projects all around the world, giving them a breadth of knowledge and experience that ensures exceptional service.
Contact the team to discuss developing a preventive maintenance plan.
Upgrades
No business can ever afford to stand still, we appreciate this fact and have developed a number of upgrade packages.
Our Account Managers are in an ideal position to provide advice on upgrades that will enable you to maintain your competitive edge.
We have cost effective packages available for the Discharge Station.
Frequently Asked Quesions
Common Discharging Questions
How often should I change the elastomers on a Discharge Station?
However, the life of an elastomer is very much dictated by the frequency of operation, the materials it comes into contact with and the cleaning regime that is used.
If you are changing your elastomers more than a couple of times a year then please contact our Aftermarket team for further assistance.
My IBC still has product remaining in it after the discharge sequence is complete?
We recommend that to maintain optimum performance the station is serviced regularly once a year.
Incomplete discharge could be a sign of problems with the internal or external vibrators.
How often do the cone seals on the Cone Valve need replacing?
We offer both factory fitted cone bonding programmes and replacement seal kits to ensure the integrity of the cone seal is maintained.
If you would like to discuss the cone resealing options available to you, please contact our Aftermarket team for assistance in your territory.
The hygiene cover has inflated.
The equipment cannot be used in this current state.
The probe on the station is slow to close.
The internal vibrator is not working.
If all of the above are OK then the hopper will need to be stripped down to check for kinks in the internal pipework or failure of the vibrator itself.
Common Blending Questions
I have oil leaking from the back of the Blender. Is this normal?
How often should the rotary seals be replaced?
The hydraulic motor keeps being started during the blending cycle is this normal?
If the motor is heard to frequently start and stop then it is an indication of an oil leak and the seals will need to be replaced.
The Blender keeps having vacuum failure alarms and will not run.
Ensure that all pipes are clear and not blocked with powder.
How can I get the best cleaning results on my discharge hopper cleaning out of place (COP)?
What’s a critical spare? What should I stock?
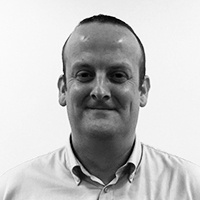
Andy Bichan
Aftermarket Manager
UK & Ireland
.webp?width=579&height=579&name=Ian-Hands-2021-B_W%20(1).webp)
Ian Hands
Service Account Manager
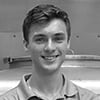
Jack Yarnall
Service Engineer
EMEA
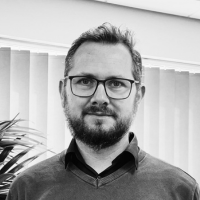
Steve Fuhrmann
Service Account Manager
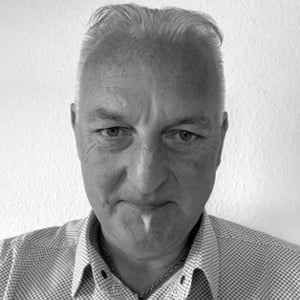
Oliver Faulk
Service Engineer
Americas
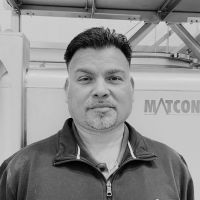
Hector Rodriguez
Service Engineer
India & Bangladesh
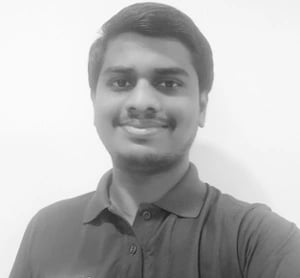
Nagendra Babu
Aftermarket & Application Support
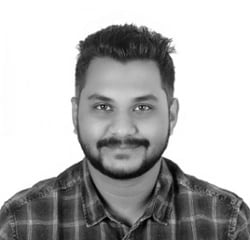
Aviroon Kanungo
Field Service Engineer
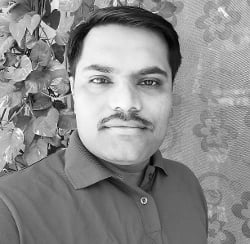
Kuldip Mochi
Assistant Manager - Aftermarket & Application Support
China, Taiwan & Hong Kong
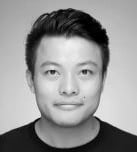
Nino Shen
Service Engineer
South East Asia & Pacific
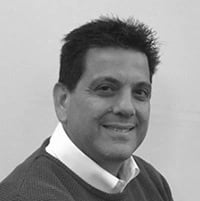
Lou Tria
Service Account Manager