Many companies have understood the conceptual advantages of using a decoupled IBC system, and have invested in conventional butterfly or slide-valve IBC technology. This works well for some companies, but for others that have very free-flowing powder blends that are difficult to handle, they are hugely disappointed with the performance achieved. The costs for a failed batch can run up to hundreds of thousands of $'s, to say nothing of the implications of a recalled batch.
Do you find that your system is often running dry on sieves or mills? Or alternatively, is your pharmaceutical equipment being flooded by material?
In this blog, we look at discharge valve choices and how you can better control the free-flowing powders in your pharmaceutical equipment…
Selecting the right IBC design for the products you need to produce and their powder material characteristics is vital and should be undertaken seriously and with due consideration. It is worth taking an in-depth look at the different suppliers available. Don’t be attracted by the cheapest price – if your powders are prone to flush then these cheap solutions probably won’t suit your pharmaceutical equipment.
Uncontrolled Flow makes Accurate Dosing Impossible
Many free-flowing products will ‘flush’ or ‘flood’ if allowed - this is a condition whereby a powder behaves like a fluid and flows uncontrollably through an outlet or feeder. Uncontrolled flow from the IBC makes accurate dosing impossible and it is difficult to feed to milling equipment or sieving if the control is not regulated.
Butterfly Valve IBCs
The well-known industry standard of butterfly valve IBCs are appropriate for powders that are easily controlled – they don’t flush and they don’t segregate (Please also read our blog on segregation and the solutions available) and they have been proven to produce the standard of product you need to match your license.
If however, your powders are very free-flowing it can be difficult to contain them with a butterfly IBC system because it is difficult to control the amount of material being fed into the downstream pharmaceutical equipment – the butterfly valve cannot easily be shut off when product is flowing. Opening the butterfly valve only slightly is very difficult. All of which results in poor product quality.
Cone Valve IBCs
The unique Cone Valve that lies at the heart of the Matcon IBC technology is proven to control very free-flowing powders. The ability to open and close the valve as required means you can regulate the amount of powder discharged from the IBC. The cone valve makes it is possible to reduce the amount of flow once material is discharging as the Cone Valve closes under gravity in the direction of material flow.
This ability to shut off flow during discharge is ideal if there is a need to change batches or there is an issue with the processing pharmaceutical equipment downstream. Also in response to level probes calling off product to provide a regular feed rate to processing equipment.
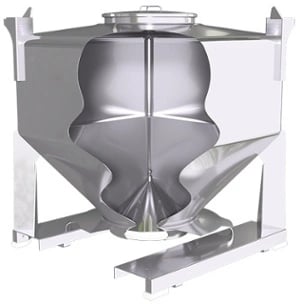
The Matcon Cone Valve technology allows even fragile products such as flakes to be gently handled.
How to Achieve a Successful Installation of Your IBC System
Achieving a successful installation of an IBC system is not just about selecting an IBC, but also lies with the experience of how to apply the technology to the various processing steps and connect it to your existing pharmaceutical equipment.
This is where the Matcon team can help, ensuring you get a system that brings you the greatest profitability and excellent product quality. We take a holistic view of your manufacturing needs and create a process of handling batches in the correct quantities optimising processing equipment and reducing the amount of manual handling needed to produce a good quality product.
To aid your pharmaceutical equipment choices, we have compiled a helpful checklist for you – we’re sure you’ll find it useful.
Posted by
Matt Baumber