No matter how experienced you are as a pharmaceutical manufacturer at some point you will encounter problems with production. These problems are usually due to either inadequate or unsuited equipment or manual operator error. A few common issues that we encounter are due to segregation of ingredients, lack of containment or reduced flow or no flow of powder from the container. In some cases this leads to ceased production whilst the problem is being fixed.
In this article we focus on the production of tablets from tablet compression equipment. The two different ways of producing tablets – either from compressing a previously granulated product or by using direct compression of blended ingredients.
Feeding powder to Direct Compression
This is the quickest and most straight forward process to use when producing tablets. An API is mixed with an excipient and lubricant, with the only processing step being blending rather than granulation. It is then fed to tablet compression with no further processing steps. Obviously it is vital that all ingredients are blended to a homogenous state with full dispersion of particles such that each tablet contains the correct dose. Segregation of ingredients is a big issue when feeding to direct compression as this will affect the uniformity of the finished tablet and risks expensive failed batches.
This is often a powder product so the flow characteristics may differ from a granulated product, if the powder can’t flow into the compression machine hopper at a suitable rate this could result in reducing the speed of the process and restrict the capacity of the factory.
These problems can be resolved by using Matcon’s pharmaceutical equipment. The unique Cone Valve technology within each of the IBCs prevents the powder forming into bridges or arches and also creates mass-flow which means that during discharge, all material is in motion, with no rat-holing or material hang up, leading to a homogenous product reaching the tablet compression hopper. To find out more about how you can eliminate your segregation issues, read our blog: ‘Quality issues of segregation and the pharmaceutical equipment to use.’
As well as no segregation of ingredients, the other benefits of using Matcon pharmaceutical equipment when direct feeding to compression are:
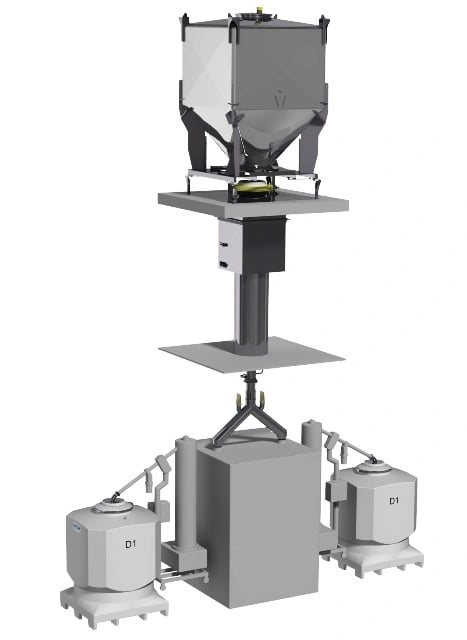
Feeding Granulated material to Compression
Currently the most common method of tablet manufacture is using granulated product, this is ether via wet granulation or roller compaction (see previous blog). Butterfly valve IBCs are more widely used in this application as the material is generally accepted to be free-flowing, however, the ability of the powder to flow freely means there is an increased risk of segregation resulting in poor tablet quality.
The Matcon Cone Valve as discussed earlier prevents the core flow seen in butterfly valve IBCs due to it creating an annular gap for discharge which results in mass-flow.
Also possessing the advantages of guaranteed flow, automatic operation and improved productivity this system ensures the manufacture of your pharmaceutical oral solid dosage (OSD) products is of the highest, consistent quality batch after batch.
Feeding across different floors
We realise that not all facilities are able to have feeding to compression on the same floor, so instead they feed through-floor across a technical space between the two GMP production areas. This can cause problems with segregation of the mix during the fall/drop between floors.
To overcome this issue, Matcon have developed a gentle transfer system. This comprises a rigid steel chute connecting the upper equipment to the tablet press. Inside, a flexible, lay-flat polymer liner is inflated just below the discharge station to create a constriction against which the powder accumulates, this is then slowly deflated allowing the powder to move as a mass, and in a controlled manner, down the chute to the tablet press below.
Please also read our whitepapers and blogs on ‘The ideal Design of Pharmaceutical Manufacturing Plant.’
Whether you are setting up a new facility or introducing new equipment to your pharmaceutical manufacturing processes. Here is a useful set of criteria you can use when choosing the supplier of your IBC systems.